How to build high end pools for wealthy clients
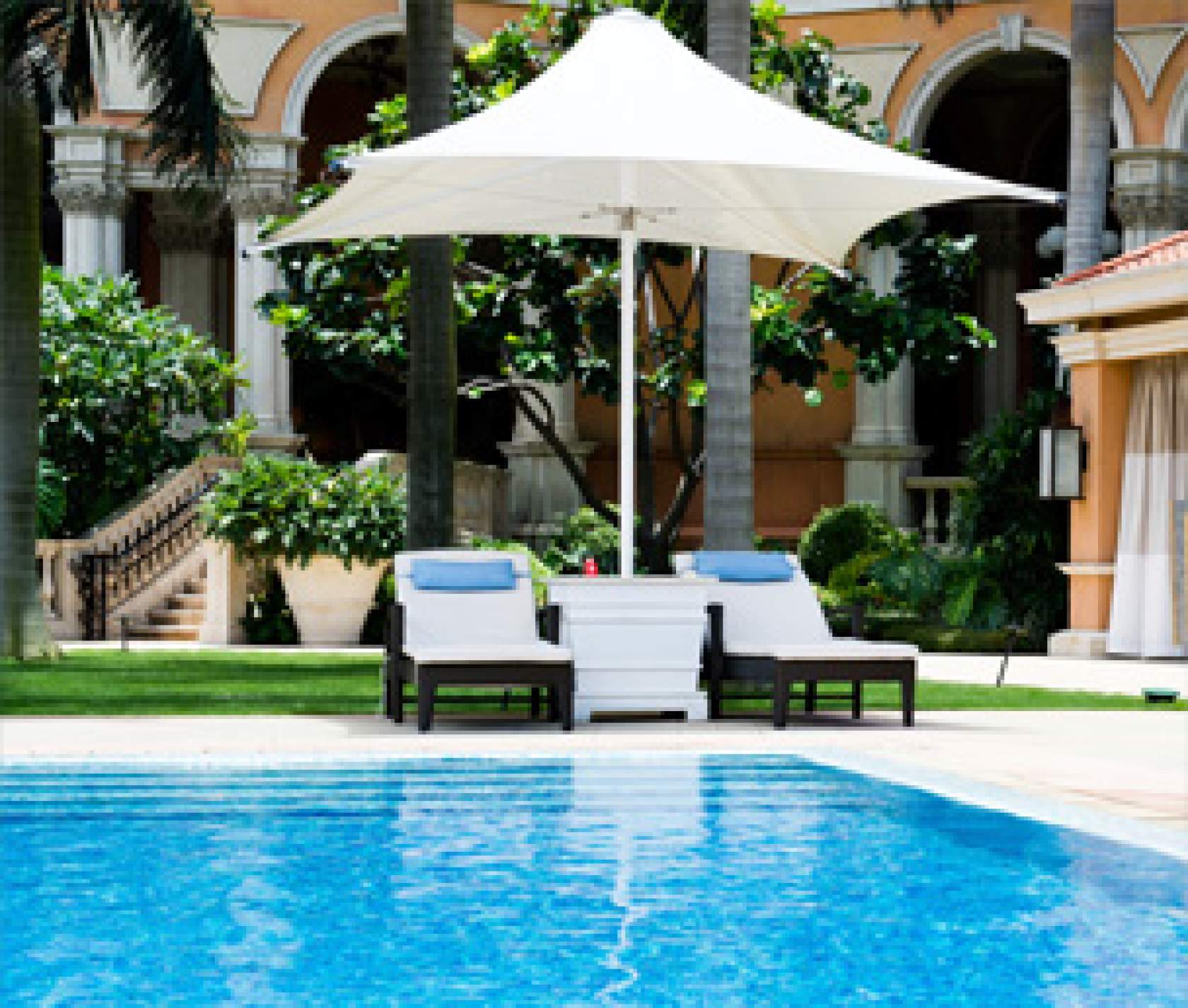
By Cal Stanley
If you aspire to build pools at the upper end of the market, there are a few things you must know and do to succeed.
First and foremost is that your customers are likely to be worth far more than you so don’t screw them around or you may find out what it’s really like to be screwed over.
These people have spent, or are about to spend, many millions on a house and land. They spend big on the best appliances and equipment they can find, they install the best furniture, the finest floor coverings and curtains. They pay for top grade landscaping and expect everything to be near perfect, pool included.
Consequently, building to an average industry standard is not going to work for them. These pools must be well above average in every respect, not only in design, materials and appearance but in the way they operate.
When selling to these customers, I found it best to assume that they would want, not just the best equipment, but the best finishing materials (eg. a fully tiled interior), the best heating system, the best cleaning system, the best pools cover, etc, etc. The best of everything. Never try and con them, they are likely smarter than you or I and have done their research on the net.
In my role as a consultant in recent years I have come across some shockers that have been built for these people.
A leaking pool
I was recently flown by the pool owner in his nice new helicopter some 250km south to look at a pool on an isolated 40 hectares of pristine virgin bush. There he had built a spectacular and very expensive house with a great view down through a valley to the Indian Ocean some 500 metres away. The pool, with a vanishing edge, was built out of ground but into an expansive deck area that overlooked this view. At first glance the pool looked fantastic because of the setting and the finish – fully tiled in glass mosaics that cost $275 per sqm before being laid.
The pool structure was designed by an engineer with little experience in swimming pools but it was structurally sound. It consisted of a concrete base and walls of brick with a reinforced concrete filled cavity. While the structure was strong enough, it contributed zero to the main aim of a pool structure. That is, to contain the water placed within it.
The interior brick walls were sand/cement rendered without any waterproofing additive. No waterproofing membrane was placed over the render. The pool was tiled and it was left to the grout to make it waterproof. Needless to say, it didn’t take long for water to begin seeping through the walls and over time ruin the exposed outer surfaces. It was actually streaming out at one spot when I was there.
The remedy for this cock-up will likely see little change out of $120,000 and don’t for one minute think that the owner – for whom such a sum is really petty cash – is going to pay one cent of it. I am glad I only had to wander back out to the helipad, fly home, write up a report and send it off with my bill.
Attention to detail
Too often I find pool that is well built and looking good until I see that horrible plastic skimmer lid sitting in the beautiful stone coping and paving.
When a pool purchaser pays a lot of extra money for stone or tile material around the pool, don’t – and I repeat – do not ever install a plastic skimmer lid that will invariably be the wrong colour and stand out like dog’s b***s or the proverbial dunny in the desert.
It is so easy to cut out a 300 mm square of the paving material, drill a 30 mm dia. finger hole in the centre and mount it over the skimmer. AS1926 now requires this lid, which cannot be locked or latched in place, to weigh 10 kg. A piece of 400 mm thick stone will likely weigh this much but if tiles are used they can be laid on a cementitious build up on top of a 4-6 mm stainless steel base plate to achieve the same weight. Either way it will look a hundred times better.
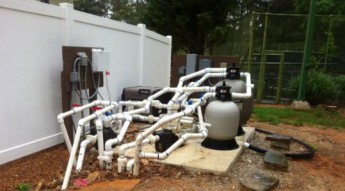
The equipment area – spaghetti junction
Many of you have seen some horrific equipment area installations. Unfortunately some of you will be guilty of creating them.
When looking at architectural plans for a new house and pool, first look at the pool and second at the area allocated for the pool equipment. It will invariably be inadequate in size and there is nothing worse than a plant room that is cluttered with no room to move. Such equipment areas often have pipes and cables going in all directions.
On a site visit recently to a $5 million house, where the pool equipment was forgotten by everyone including the pool builder, it was found that the allocated space could hold less than half of the equipment in the contract. In fact it could only accommodate the spa gas heater and one pump. A storeroom off the garage one floor below had to be commandeered for the rest of it. Incidentally it also seems that the pipework wasn’t pressure-tested as there is a leak somewhere – impossible to get at now without some serious jack hammer work and great expense.
Many pool builders do not produce a scaled layout plan of the pool equipment area. Such a plan is essential to ensure the space allocated is sufficient and to give the equipment installers a blue print to work to.
Many use one crew to run the pipes from the pool and another to install the equipment. This scenario usually causes pipes to be terminated in the wrong location for the equipment. They are then relocated above ground (it’s easier) to the correct position and when completed we have pipework that looks like spaghetti but doesn’t taste anywhere near as good. At the very least, this is highly unprofessional.
Relocation of all pipes should be done below ground, only bringing them up where they are to be used to provide a neat and accessible area for the owner. If that is through concrete early in the job then use that scaled equipment area plan to get them in the right spot.
Equipment areas are often hidden and forgotten. Hide them by all means but never forget the vital role they play over many years of pool use.
In conclusion
Unfortunately similar scenarios and mistakes are all too prevalent in our industry. Common sense will tell you that these sorts of issues shouldn’t occur with any pool installations, however they are even less excusable when building at the top end of town. The real answer is to make certain you charge enough to be able to carry out every facet of the job correctly – then do so.
For these articles Cal Stanley draws on his 30 years’ experience and success in pool construction, having run award-winning pool construction company Neptune Pools in Western Australia for three decades. For the past five years he has worked as a pool consultant and trainer and delivers hydraulics courses for the swimming pool industry. If you have a topic you think Cal should delve into, contact him on: neptunepools@westnet.com.au.