Tips for tiling pools in hot weather
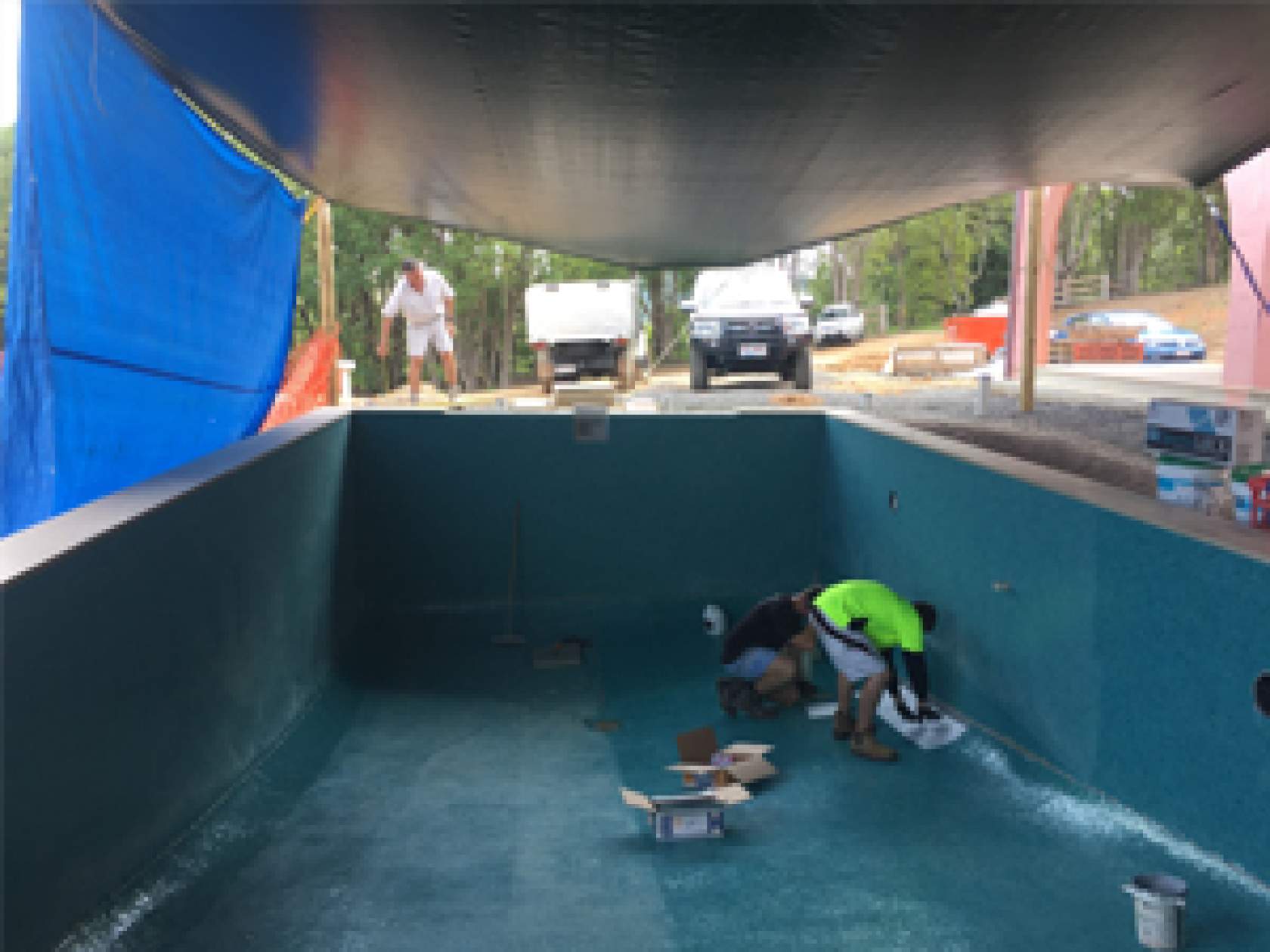
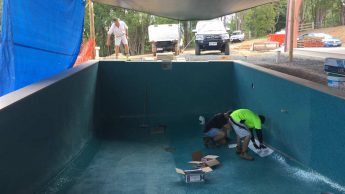
Laticrete offers some tips for care with mortar during summer.
Conventional Portland cement tile-setting beds, thin-set mortars, cement plasters and stuccos are often permanently damaged when subject to hot, dry temperatures or desert climates immediately after installation.
High temperatures remove the water content of the mortar required for Portland cement hydration, curing and strength development. In addition, rapid drying often causes mortar to crack, crumble or lose bond. Waterproofing membranes, anti-fracture membranes, epoxy adhesives, epoxy grouts, epoxy waterproofing membranes and most other products will also be affected by hot working temperatures.
Flash setting and reduced working time can result. It is important to note that surface temperature is more important than air temperature. Therefore, monitor the surface temperature of the installation.
There is a simple rule to follow when an installation is subjected to high temperatures, the 8⁰C Rule: For every 8⁰C above 21⁰C, Portland cement and epoxy based materials take half as long to cure.
The use of premium latex-fortified mortars e.g. 254 Platinum Adhesive or 315 Super Floor & Wall Adhesive gauged with 4237 Latex Additive allows installations to be made at higher temperatures due to the fact that they have longer working properties. 3701 Mortar Admix in thin-sets, plasters, stuccos and other Portland cement mortars allow work to continue in hot weather without costly delays or damage. Installations can be made in temperatures as high as 32⁰C under normal circumstances.
Laticrete Latex Fortified Mortars are not damaged by high temperatures and thermal shock after placement and eliminate the need for wet curing. Rapid setting materials will provide for greater challenges when working in high temperatures and should be used with caution.
General tips for working in hot temperatures
1. For best results, always ship and store installation materials at 5⁰C to 32⁰C to extend the shelf life and working time. Do not store products in direct sunlight. If installation materials are too warm, they should be cooled to the specified temperature range for that specific product.
2. Dampen or wet down substrate surfaces to not only clean the area, but to lower the temperature and lower the absorption rate of the substrate. Sweep off excess water just before mortar is applied. This step will extend the working time of the installation materials.
3. Stir latex additives thoroughly before mixing with thin-sets, grouts, plasters, stuccos and other Portland cement mortars.
4. Due to the rapid rate of moisture loss and Portland cement dehydration at temperatures >32⁰C, cover installations with polyethylene sheeting for 1-2 days to allow curing at a more normal rate.
5. Low humidity also accelerates the curing process.
6. Tent off or provide shade when working in direct sunlight.
7. Work during cooler periods of the day (e.g. early morning).
Tips for grouting in hot temperatures
1. Store grouting materials at 5⁰C – 32⁰C to extend the shelf life, pot life and working time. Do not store products in direct sunlight. If installation materials are too warm, they should be cooled to the specified temperature range for that specific product 24 hours prior to the start of grouting.
2. Dampen or wet down substrate surfaces to not only clean the area, but to lower the temperature and lower the absorption rate of the substrate.
3. Always clean the mixing pail before mixing a fresh batch of grout. Left over grout in the pail (on bottom and sides) can accelerate the setting of freshly mixed grout.
4. Mix cement grouts with clean cool water. This step will extend the pot life and open time of cement grouts.
5. Remix cement grouts after 15 to 20 minutes (after initial mixing, 5 minutes of slaking/remix and use) to an even consistency to prolong pot life.
6. Tent off areas of work to provide shade when working in direct sunlight.
7. Work during cooler periods of the day (e.g. early morning).